技術資料technical data
ZAPシート
1.底面の防食
- 被防食材:機械加工した鋼材
- 防食材:ZAPシート
- 暴露環境:準工業地帯(埼玉県上尾市)で屋外暴露
- 暴露期間:6ヶ月
試験方法
ZAPシートによる底面防食
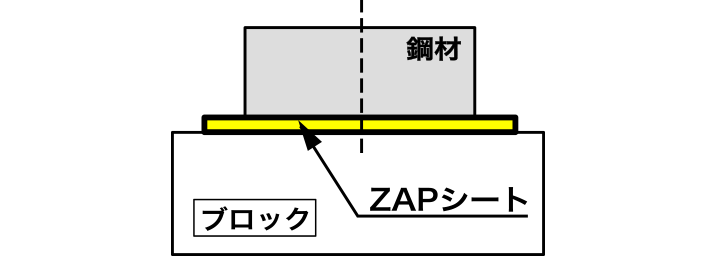
無防食
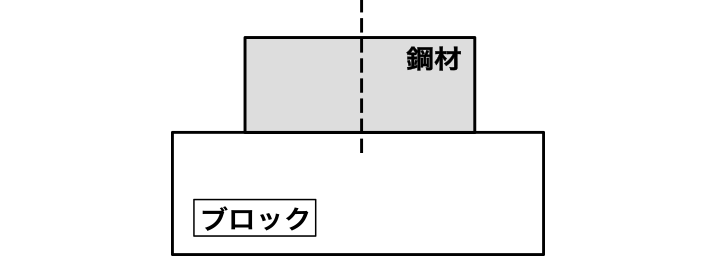
試験結果
ZAPシートによる底面防食
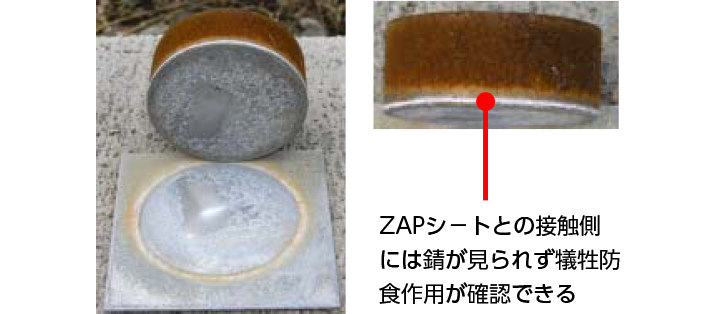
無防食
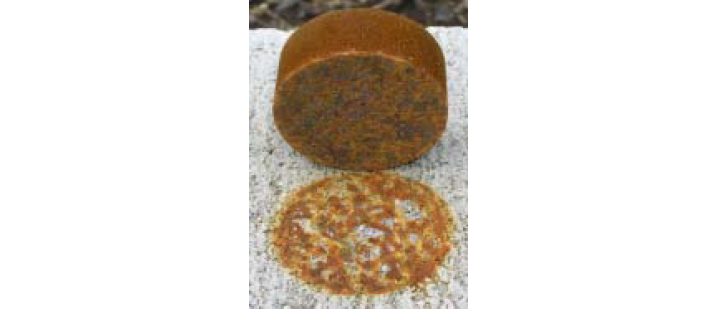
2.配管架台防食へのZAPシートの適応
ZAPを配管と配管架台間に挟んで使用した場合の防食性能を把握する
試験条件
- 被防食材
鋼管:配管用炭素鋼管
架台:溝形鋼 [何れも購入時の黒錆は保持したまま試験に供す] - 供試材(配管防食材)
ZAPシート:配管と架台接触部間にZAPシート(2.0t)を使用したもの
無防食:配管と架台接触部間に防食手段を何も実施しなかったもの - 暴露環境:準工業地帯(埼玉県上尾市)で屋外暴露
- 暴露期間:屋外暴露 / 場所:埼玉県上尾市 / 期間:2年
試験方法
防食を一切講じていない配管用炭素鋼管と溝形鋼の架台間にZAPシートを挟み込み、屋外環境に暴露した(図参照)。また無防食はZAPシートを挟まないことで再現した。
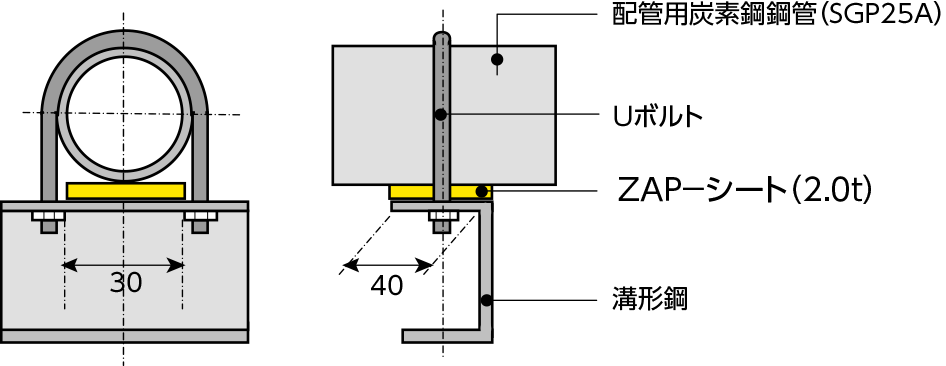
試験結果
ZAPシート施工品:ZAPシート接触部
鋼管
- ZAPシートとの接触部は、鋼管表面に光沢が観察されるなど完全に錆発生が抑制されていた(図.1)。
- Zまた接触部の周辺は、白錆、もらい錆が見られるが、幅方向では雨水が多く溜まるため"約18mm"の広い範囲で、 長さ方向では"ZAPシート長+約5mm"の範囲で、亜鉛の犠牲防食作用により良好な防食状態が維持されていた(図.2)。
架台
- 鋼管と強く接触した部分は鋼管と同様に、錆発生は完全に抑制されていた(図.3&4)。
- またZAPシートとの当たり面には、白錆が見られるが、赤錆は全く観察されず良好な防食状態を維持していた(図.3&4)。
- ZAPシート当たり面の周囲は、犠牲防食効果で幅2mm以上防食されていた(図.4)。
ZAPシート
- 厚み減少は、10μm以下であった。
無防食品
鋼管・架台
- 鋼管、架台接触部は、初期の黒錆が僅か観察され、錆の程度は比較的軽いが、その周辺は何れも錆が進行していた(図.5&図.6)。
結論
上記より、配管と配管架台間にZAPシートを挟み込むと、その接触部とその周辺が防食できる。
3.塩水噴霧環境における地際(根元)防食へのZAPシートの適応
試験条件
- 被防食材:ブラスト処理した配管用溶接鋼管
- 防食材:ZAPシート(板厚=1.0mm)
- 暴露環境:塩水噴霧試験(JIS Z2371に準拠)
- 暴露期間:2000hr
試験方法
ZAPシートで防食した溶接鋼管
- モルタルに埋設した溶接鋼管(ブラスト処理済み)の地際(根元)部の回りに半円筒状のZAPシート 2個をステンレスバンド、締付金具で固定する。
- 次に、最下部をZAPペーストでコーキング処理し上記環境に暴露した。なおZAPシート間の隙間a部は、ZAPペーストによるコーキング処理は行わず、そのままとした。
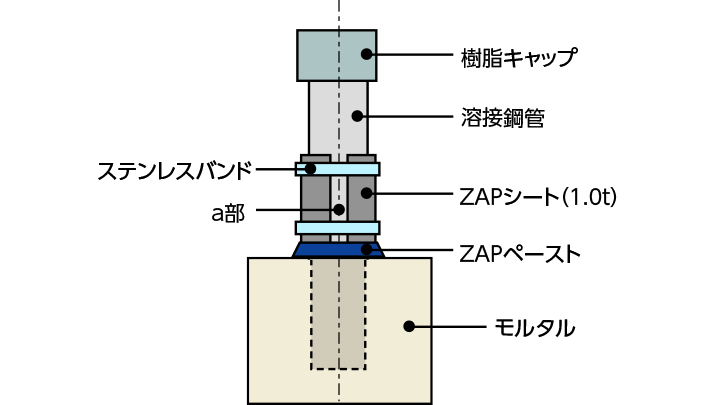
裸の溶接鋼管
- モルタルに埋設した溶接鋼管(ブラスト処理済み)を上記環境に暴露した。
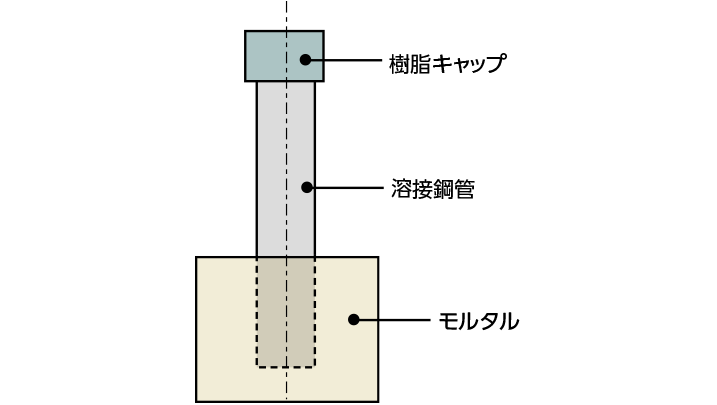
試験結果
ZAPシートで防食した溶接鋼管
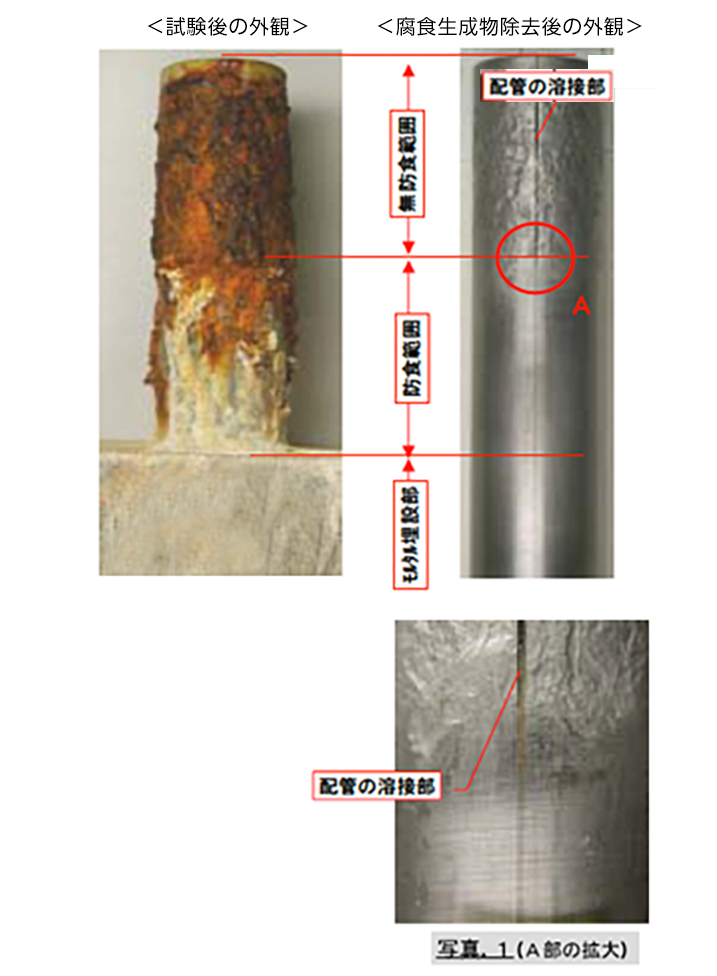
裸の溶接鋼管
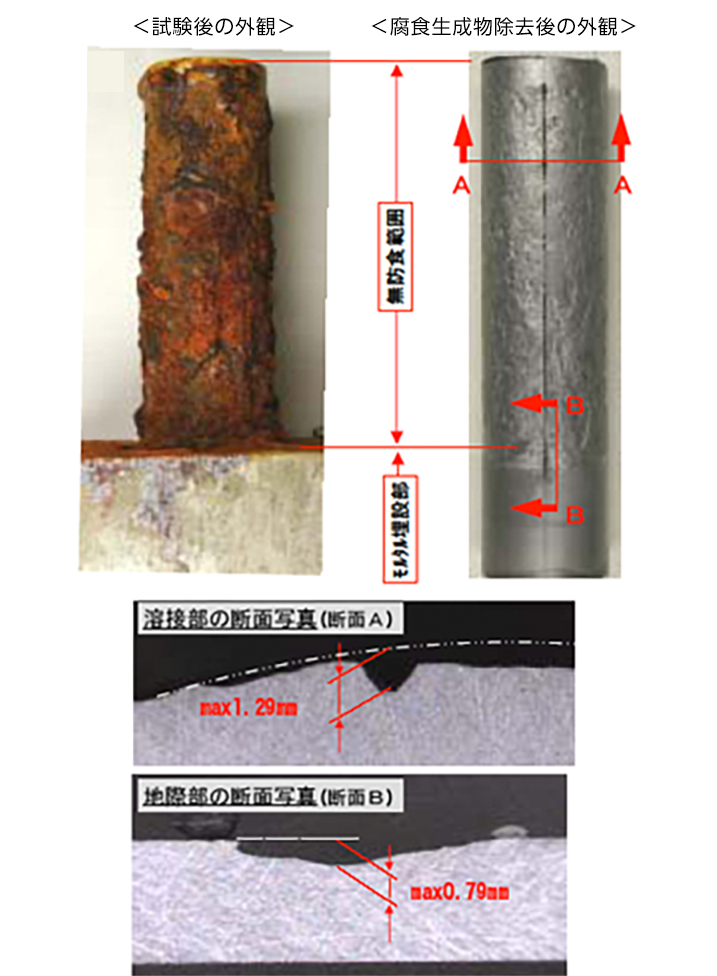
評価
ZAPペーストで防食した溶接鋼管
- 鋼管上部の無防食部では全面が激しく腐食するだけでなく、溶接部が溝状に局部腐食し腐食深さが0.75mmに達していた。
- 一方、防食部には侵入した塩水による白錆が観察されたが、亜鉛の犠牲防食作用により溶接部やZAPシート間の隙間(上記試験方法のa部)を含め腐食は全く見られず、初期の状態を維持していた。
- 防食部の腐食深さ(写真.1参照)
・鋼管最大腐食深さ=0mm
・溶接部最大腐食深さ=0mm
裸の溶接鋼管
- 鋼管は全面激しく腐食するだけでなく、その溶接部は溝状に局部腐食し腐食深さが1.29mmに達していた。また地際部は0.79mmの深さまで腐食が進んでいた。
- 防食部の腐食深さ(上記断面写真参照)
・地際部最大腐食深さ=0.79mm
・溶接部最大腐食深さ=1.29mm
4.土壌中環境における地際(根元)防食へのZAPシートの適応
試験条件
- 被防食材:ブラスト処理した溶接鋼管(SGP25A)
- 地際防食材
ZAPシート:防食材としてZAPシート(1.0t)を使用したもの
無防食:地際部に防食手段を何も講じなかったもの - 暴露環境:屋外土壌埋設、場所は埼玉県上尾市で、土壌は黒土で、含水比約35%、pH6.0
- 暴露期間:3年
試験方法
図のようにブラスト処理した溶接鋼管において、地際及び土壌中の範囲Aに防食材を施行した後、屋外で土壌中に一部を埋設しその防食性能を把握した。
また、ZAPシートの平均消耗速度は、輪切りにしたイ~オ部について次式にて算出した。ここで亜鉛密度は7.13g/cm3とした。

なお、鋼管上の錆は市販の剥離剤で除去した。
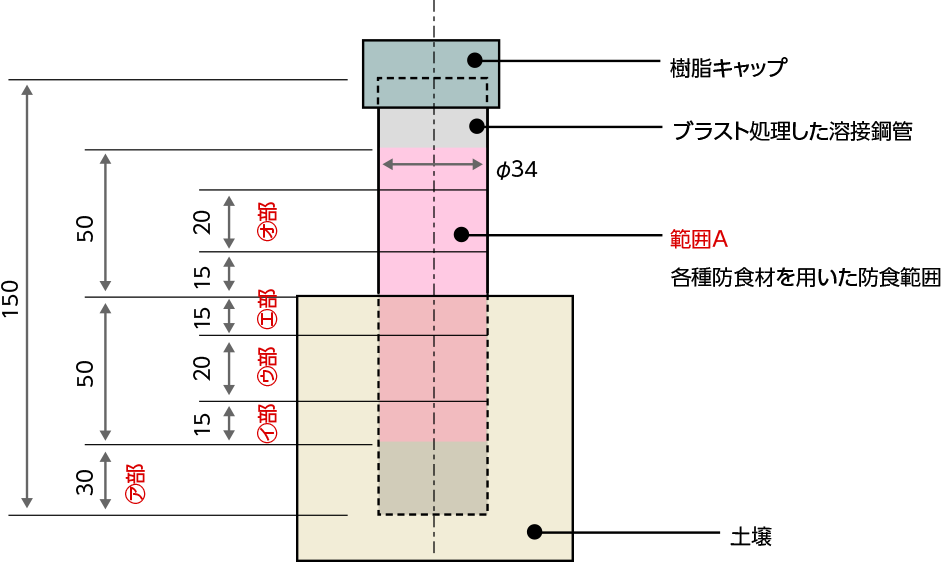
試験結果
ZAPシートで防食した溶接鋼管
-
防食仕様
地際防食材として高純度亜鉛板であるZAPシートを用い、下図のように半円筒形のZAPシート2枚に隙間を設けて、鋼管回りにステンレスバンド、締付金具で固定し、一部を土壌中に埋設した。
-
3年後の外観
防食材除去後
- 大気中の無防食部では赤錆が発生している。
- 一方、防食部や隙間Z部には上部から侵入した『もらい錆』や軽微な赤錆が僅かに観察されるが、亜鉛の犠牲防食作用や被覆防食作用により全体的には良好な防食状態を維持している。
- 更に土壌中の無防食部(ア部)も亜鉛の犠牲防食作用で錆発生は極少量に抑制されている。
錆剥離後
- 赤錆除去部には軽微な肌荒れや局部腐食が僅かに観察される程度で、良好な防食状態が保持されていた。
局部腐食はZ部近辺を中心に数カ所見られ、深さは30μm以下であった。 - 平均消耗速度の表ZAPシートの消耗速度を右表に示す。
従って、期待耐用年数は20年以上あるものと推定される。
なお、イ部の消耗速度が大きいのは、地中の無防食範囲ア部に対する犠牲防食作用が活発に生じるためである。
平均消耗速度
- イ:30μm/年
- ウ:10μm/年
- エ:7μm/年
- オ:5μm/年
無防食の溶接鋼管
-
防食仕様
-
3年後の外観
試験終了後
- ブラスト処理溶接鋼管は大気中、土壌中何れも赤錆が見られ、特に土壌中は大気中に比べ錆発生が進んでいる。
錆剥離後
- 土壌中の局部腐食は、溶接部を含め多数観察され、最大で深さ816μmに達しており、その腐食速度は約270μm/年と算定された。
- また土壌中の鋼管を輪切りにして試験前後の重量差から平均腐食速度を算出すると20~35μm/年であった。
結論
ZAPシートを防食材として地際部に使用すると同部の錆を大幅に抑制することが可能になる。
5.ステンレス板の隙間腐食に対するZAPシートの効果
試験条件
- 被防食材:ステンレス板/SUS430(1.0t)
- 防食材
ZAPシート:ステンレス板間にZAPシート(1.0t)を挟み込んだもの
無防食:地際部に防食手段を何も講じなかったもの - 暴露環境:塩水浸漬/濃度 5wt%NaCl水溶液/温度 35℃
- 浸漬時間:2000hr
試験方法
1.0mm厚のステンレス板(SUS430)間に1.0mm厚のZAPシートを挟み込み、M5のステンレス製のボルト、ナットにより、トルク15kgf・cmで締付けた。また無防食はZAPシートを挟まないことで再現した。次に供試材を5wt%の塩水の入ったバット中に35℃の環境下で2000hr浸漬した(図参照)。
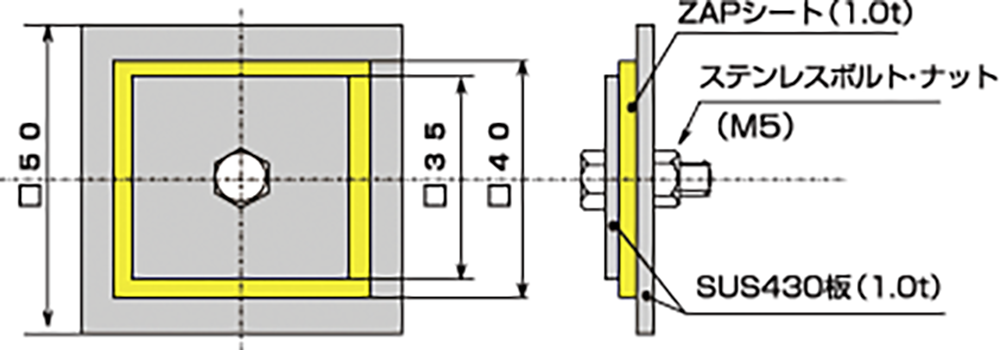
試験結果
ZAPシート施工品
試験後の外観
- 亜鉛の白錆が全面に観察される(図.1)。
合わせ面のステンレス板表面
- 土合わせ面のステンレス板表面には亜鉛の白錆が部分的に観察されるが(図.2)、白錆を除去(※)したステンレス面には亜鉛の防食作用によって光沢が観察されるなど、錆は全く見られず、隙間腐食は完全に抑制されていた(図.3)。
※ステンレス板を10vol%酢酸アンモニウム水溶液中(70℃)に浸漬し除去した。
-
-
合わせ面のステンレス板表面白錆除去前合わせ面のステンレス板表面白錆除去後
無防食品
試験後の外観
- 上側ステンレスの周囲に赤錆が観察される(図.4)。
合わせ面のステンレス板表面
- 合わせ面のステンレス板には上側、下側のステンレス板とも同位置に、隙間腐食によって長さが0.5mm以上の大きな局部腐食は、7箇所、また0.1mm程度の小さいものも、若干観察された(図.5)。
- また下表に示すように、大きな局部腐食の深さは、最大が854μmと板厚の85%に至った(図.6)。
局部腐食の深さ
B:80μm
C:854μm
D:178μm
E:98μm
F:617μm
G:451μm
※デプスゲージで測定
-
-
合わせ面のステンレス板表面
結論
ステンレス板間にZAPシートを挟み込むことによって、ステンレス板の隙間腐食が防止できることが判る。
6.アルミニウム材と鋼板間の異種金属接触腐食に対するZAPシートの効果
試験条件
- 被防食材
ブラスト処理した冷間圧延鋼板(SPCC 1.0t)
アルミニウム材には純Al系のA1050製のワッシャを使用 - 防食材:ZAPシート(2.0t)
無防食:地際部に防食手段を何も講じなかったもの - 暴露環境:塩水浸漬/濃度 5wt%NaCl水溶液/温度 35℃
- 浸漬時間:500hr
試験方法
アルミニウム製ワッシャとブラスト処理した1.0mm厚の冷間圧延鋼板との間に2.0mm厚のZAPシートを挟み込み、M8の樹脂製(ポリカーボネイト製)のボルト、ナットにより、トルク1.0N・mで締付けた(図参照)。また無防食はZAPシートを挟まないことで再現した。
次に供試材を5wt%の塩水の入ったバット中に35℃の環境下で500hr浸漬した。
また腐食によるワッシャの重量変化率は、次式で求めた。なお試験後のワッシャ重量は、酸にて腐食生成物を除去後、測定した。

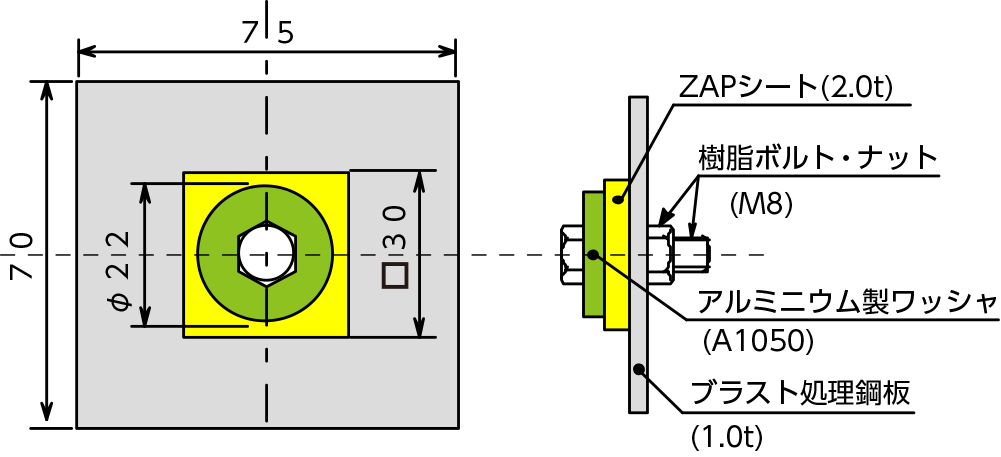
試験結果
ZAPシート施工品
試験後の外観
- 亜鉛の白錆が全面に観察された。 (図.1参照。但し図1は、試験後水洗したため一部白錆が脱落している)
- 酸で白錆を除去した後の外観を図.4に示すが、腐食の形跡は全く観察できず、ZAPシートの犠牲防食作用で腐食が完全に防止されていることが判る。
アルミニウム製ワッシャ
- 図.2、3に示すようにワッシャには腐食は全く観察されず、ZAPシートの犠牲防食作用により鋼板と共にアルミニウム製ワッシャも完全に防食されたことが認識できる。
- またワッシャの重量変化率は、0.1%以下と僅少で誤差範囲内レベルであった。
-
-
合わせ面のステンレス板表面ワッシャ合わせ面のステンレス板表面白錆除去後の鋼板
無防食品
試験後の外観
- 図.5に示すように、アルミニウム製ワッシャによる犠牲防食作用でワッシャの周囲約10mmに白錆が見られたが、その外側にはほぼ全面赤錆が観察された。 高純度亜鉛板であるZAPシートに比べ、アルミニウムの犠牲防食の範囲が大幅に狭いことが把握できる。
アルミニウム製ワッシャ
- 図.6、7、8に示すようにのボルト側のワッシャ表面や端面には局部腐食が多数見られ、鋼板とアルミニウム製ワッシャ間の異種金属接触腐食でアルミニウム製ワッシャが腐食したことが判る。
- またワッシャの重量変化率は、ZAPシートを使用した場合に比べ大きく、13.2%に達した。
-
-
合わせ面のステンレス板表面
結論
上記より、鋼板とアルミニウム間の異種金属接触腐食はZAPシートの使用によって、完全に防止できることが判る。